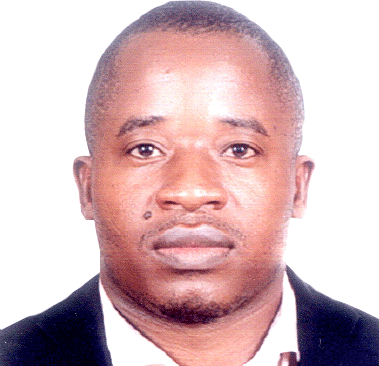
Every business set up has a supply chain process. The difference between successful businesses and unsuccessful ones lies between how well the business understands and manages its supply chain flows. The three super critical supply chain flows are information, product and funds.
Supply chain management with Gibson Sibanda
Information plays an important role in supply chain management. It is a cross functional driver of supply chain as it cuts across all supply chain drivers and network partners. Sharing and coordination of information flow among supply chain members should be done properly as failure to do so leads to bullwhip effect. Bullwhip effect is the distortion of information about product demand across the supply chain network and tends to increase as the distance between the source of information and the final receiver widens. The result of bullwhip is increased inventory, and to those who understand operational excellence, excess inventory is one of the sources of waste in a business. Some businesses fail due to excessive information gaps in their operations. Information gap is when customers do not know about the availability or source of products, and suppliers do not know about their potential customers.
A product comes in the form of raw materials, work in progress and finished product. It flows from the inbound side to the outbound side for the purposes of delighting the consumer in a supply chain. An organisation might have a very good product but still fail to succeed as a business due to inefficiencies and improper coordination to reach its customers. Improper product flow strategies lead to other three logistics of business gaps namely time, space, and quantity. Time gap is when there is a difference between the time a product becomes available and the time customers want to buy it. A good example of time gap management is done by whisky manufacturers where it takes several years from distillation to maturity and consumption. Missing a single production cycle means there is no supply of the product in relation to that cycle pattern, ultimately leading to loss of revenue. With regards to space gaps, not all product(s) are confined within a single geographical area of the business operation, hence the space gap needs close attention. This gap happens when suppliers are physically separated from customers, in some cases the locations being continents apart. This is a challenge for many businesses as their sourcing strategy might fail to recognise the gap, leading to either inventory stock outs or overstocking. Space gaps are not too far away from quantity gaps either. A quantity gap is the difference in amounts of stock available from suppliers and the demand from customers. Procurement practitioners in such business operations should use their supply chain trade off skills effectively. Successful supply chain practitioners replace inventory with information and move away from supply chain management to demand management.
In contrast with other supply chain flows, funds flow in the opposite direction of the product. Funds flow from the right to the left, which is from the outbound to the inbound side of the supply chain. Funds are a creature by supply chain partners as a result of supply chain surplus from value generating activities. For network members to create supply chain surplus, they should build strong and sustainable supply chain relationships. Sharing of information is the cornerstone of an effective relationship. As such, the success of a business lies in the effective management of supply chain flows and as exposed by the article, supply chain professionals play a big role in supply chain mapping, information sharing and product movement across the supply chain.
Gibson Sibanda is a member of the Chartered Institute of Procurement and Supply (MCIPS), secretary of CIPS Zimbabwe branch. The views expressed in the article are entirely personal. For feedback you may contact him on [email protected]