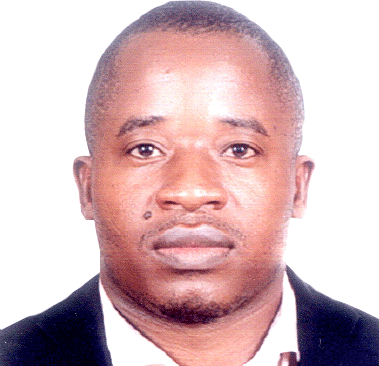
Procurement constitutes an average of 65% to 75% of many organisations’ expenditure. In tough economic situations, there is a continuing need for procurement professionals to implement and manage cost reduction programmes. As many organisations continue to search for opportunities to reduce costs, there should be an agreed, and well-defined programme for and by supply chain professionals to cut costs. The following initiatives are possible contributions which procurement practitioners can adopt to reduce and contain costs.
supply chain management with GIBSON SIBANDA
Challenge specifications or designs
Specifications are the detailed statement of the needs by the user. In many instances, these are not thoroughly or systematically analysed. From experience, I have noticed that users draw specifications with a supplier in mind, hence they give little room for consideration of alternatives. There are two approaches to specifications, which are conformance and performance. The former are clear and unambiguous laid-down requirements. They are detailed about the product and not the application, restricts innovation, technical in nature and are not negotiable. On the other hand, the latter provides a clear indication of the function, application the performance expected and supplier is allowed to offer an appropriate product. It allows wider competition and enables suppliers to suggest new or improved ways of meeting the product. These are outcome-oriented. Procurement policies and procedures should be clear as to instances when either of the two should be applied. Conformance specifications lead to a certain brand preference whereas performance specifications overlook the brand. In a drive to reduce procurement costs, performance specifications give a wide room for alternatives and allows for early supplier involvement. Performance specifications allows the use of concurrent engineering, implementation of “design for lean” and use of value analysis methodology. Performance specifications facilitate easy adoption of the 80%/20% cost rule analysis.
Challenge existing contracts for price competitiveness
Contracts which have been in existence for a long time are other avenues for possible cost reduction. Contracts that were drawn say five years ago if reviewed will show opportunities for cost reduction. Economic situation at the time when the contract was drawn could be different, hence a review will lead to huge savings. This is very real in situations where there are changes in consumption, volatile market conditions and unstable currencies. In other situations, having a long-term contract with set and agreed review conditions leads to cost reduction. Long-term contracts facilitate effective planning and ultimately benefit on the economies of scale. During a review of existing contracts, thorough research is important as it helps in benchmarking the market. When challenging existing contracts for competitiveness, there is need to establish cost drivers that are tailor-made to target your negotiations to high impact cost drivers.
Adoption of standardisation
Variety reduction helps in keeping the amount of inventory at a minimum. Take for instance an organisation with a single brand of vehicles; this firm can do with minimum stock items for a wide range of fleet as opposed to an organisation with say five brands of vehicles. Spares compatibility will mean that a firm with one brand will only stock minimum spares for use by any vehicle, thereby keeping stock holding costs at very low levels. Economies of scale can be easily achieved during the sourcing process. Supplier relationship management is improved. Use of a single supplier range is made possible and helps in designing duplicate ranges.
- Chamisa under fire over US$120K donation
- Mavhunga puts DeMbare into Chibuku quarterfinals
- Pension funds bet on Cabora Bassa oilfields
- Councils defy govt fire tender directive
Keep Reading
Challenge supply chain costs
Carrying out supply chain mapping is very important in determining costs at every stage of the supply chain. For those organisations sourcing from abroad, they should take time to scrutinise the implication of international commercial terms (incoterms) in use. Improper acceptance and use of wrong incoterms will only add costs to the supply chain. Instead of paying insurance cost per every shipment through say cost, insurance, freight, why not have a blanket insurance for all the annual shipments. Carrying out a value analysis on the packaging costs can go a long way in eliminating unnecessary costs. Procurement planning helps reduce costs by ensuring use of effective and efficient mode of transport. Poor procurement planning leads to emergency procurements, hence fast and expensive mode is always the default transport system, thereby increasing costs.
Eradication of uncompetitive suppliers
Cost-cutting and containment opportunities should be communicated to suppliers. Those who are found not taking steps to reduce costs should be removed from your database. Sustainable cost reduction initiatives come from the suppliers as they have best knowledge about of cost drivers. A review of the existing sourcing policy helps identify opportunities. In some cases, competitive tendering helps to find new and competitive suppliers while single sourcing can provide economies of scale benefits. Challenging the status sourcing strategy and carrying out cost benefit analysis is a good practice.
Consideration of outsourcing
Outsourcing is a management strategy by which major non-core activities or functions are transferred to specialist, efficient, external providers. Central to the strategy is make or buy decisions. Certain huge capital procurements are better outsourced. When making outsourcing decisions, the total costs of ownership takes centre stage. The three steps of outsourcing involve selecting non-core activities, conducting a market test and finally setting sights high. The most popular outsourced services in Zimbabwe by the manufacturing sector is security, canteen services and a little bit of transportation and distribution services. Ironically, the major non-core functions in manufacturing sector by value is transportation and distribution, of which it the one with little consideration locally.
Better use of working capital
Procurement professionals play a huge role in management of the organisation’s working capital. Properly negotiated payment terms will go a long way in ensuring a firm’s viability. At a bare minimum, advance payment systems should be avoided only and unless if it’s part of a supplier development practice. Working capital management through inventory reduction helps to contain costs. In manufacturing organisations, adopting build-to-order systems as opposed to the make-to- stock system, has a huge impact on costs.
Procurement centralisation
The procurement function should be centralised as this facilitates proper expenditure analysis. With a devolved procurement structure, duplication of purchases is high, hence opportunity areas become hidden. Economies of scale are difficult to make use of. Supplier rationalisation strategies leads to increased competition thereby reducing costs. It also helps in strategic supplier relationship management. In a centralised environment, staffing requirements are reduced and it leads to creation of expertise through category management. Procurement segmentation facilitates proper formulation of a clear category sourcing strategy.
Gibson Sibanda is a member of the Chartered Institute of Procurement and Supply (MCIPS), general secretary of Cips Zimbabwe branch. The views expressed in the article are entirely personal. For feedback you may contact him on [email protected]