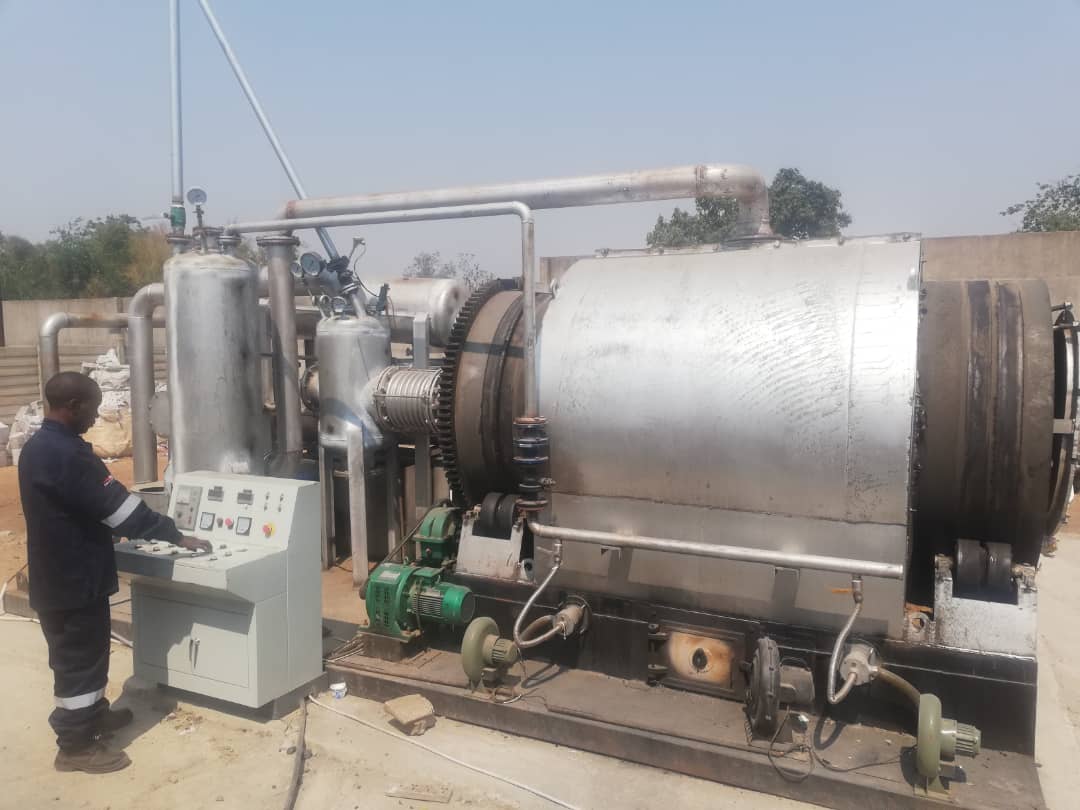
A year after winning the Total Zimbabwe start-up challenge with an innovative idea to turn waste into diesel, Farai Masendo says his business has taken off and is planning to spread his wings across the country.
Masendo (FM), Pyro Energy founder and CEO, told our reporter Fidelity Mhlanga (FS) that his firm had set up a plant in Harare’s Ardbennie industrial area, which was producing 200 000 litres of diesel a month.
In the wide-ranging interview, the upcoming entrepreneur said through his innovation, he had created 250 jobs and his ambition was to cut Zimbabwe’s fuel import bill by at least 30%.
Below are excerpts from the interview.
FS: Can you give us an overview of Pyro Energy?
FM: Pyro Energy is a waste-to-energy company, which is pioneering recent waste, chemical and renewable energy technologies to produce diesel from waste plastics and used tyres.
Through these technologies, the company has optimised its production costs and is currently selling its diesel at US$0.65 versus the average market price, which is currently at US$0.90.
The byproduct from the process is wax, which we use to produce affordable and excellent quality floor polish.
- Chamisa under fire over US$120K donation
- Mavhunga puts DeMbare into Chibuku quarterfinals
- Pension funds bet on Cabora Bassa oilfields
- Councils defy govt fire tender directive
Keep Reading
Application of the diesel includes both internal and external combustion engines, rotary kilns, power generation, industrial dryers, boilers, burners, generators and lubrication.
FS: What developments have you made since winning the Total start-up challenge in 2019?
FM: After winning the start-up challenge, I have managed to invest the funding I got from Total Zimbabwe into my business.
I have managed to design, install and successfully commission a new world-class production plant with a larger production capacity/throughput, thus upgrading our diesel output to at least 200 000 litres per month.
The new plant has also improved the diesel quality as well as recovery yield from the waste tyres and plastics.
The company is also in an expansion drive to set up 10 similar plants across Zimbabwe in the next year so that we decentralise our operations to every city/town and recover value from waste plastics and tyres that are in those areas as well as creating more jobs.
To date more than 250 direct and indirect jobs have been created through our operations consisting of waste collectors and segregators.
We also have graduates and interns in our production and quality departments FS: Have you modified your machinery and what kind of technology are you using now which is different from the previous machinery?
FM: Both machines use the pyrolysis technology. However, the current machine is different from the previous one.
It is automated and runs on programmable logical controllers (PLCs). It is also less manual compared to the previous one.
It has better ergonomics to promote the safety of machine operators.
The current machine also ensures that the process takes place in an environmentally friendly way and complies to the environmental management regulations.
The new plant has also improved the diesel quality as well as recovery yield from the waste tyres and plastics.
Plans are also in place to generate electricity from that same machine, making it self-powering for all components of the plant that use electricity.
The new plant also allows the easy application of artificial intelligence in the system for process optimisation.
FS: Can you take us through the waste-fuel conversion process.
FM: The process starts from shredding of raw materials, which are waste plastic and tyres.
This is important as it improves the efficiency of our process.
After shredding, the raw materials are taken into our production line for processing.
The processing takes place in the absence of oxygen, thus ensuring that no toxic gases or greenhouse gases will be produced from our process.
The process is also aided by our locally developed catalyst, which has greater impact in increasing the diesel yield from the waste plastics and tyres FS: What is the market perception of your diesel?
FM: Due to our dedicated team of engineers, our company is delivering a quality product, which is within specifications to our customer requirements.
The only issue that the company is currently working on is to meet the diesel demand, which is very high at the moment.
FS: Tell us about how and where you collect your inputs.
FM: We collect from different dumpsites and landfills across Harare, thus promoting sustainable environment and waste management.
We also collect the waste from different suburbs across Harare.
We have also partnered with other companies, which we are providing with waste collection/disposal services for their waste plastics and tyres free of charge.
The company also engages the community on different awareness sessions on the importance of waste segregation at home and the importance of sustainable environmental/waste management for future generations.
We are also looking for different partners/players to join us on our raw materials supply chain all over Zimbabwe.
FS: Have you found investors or fresh capital to inject into your business?
FM: I have just successfully commercialised my innovation.
Therefore, funding from different government departments as well as both local and international sponsors is welcome so that the company makes greater impact and covers as much ground as possible.
FS: What opportunities are you seeing during this period of economic challenges?
FM: The company falls under essential services and we have been running while at the same time abiding by Covid-19 regulations guided by issued statutory instruments.
FS:What is your five-year plan?
FM: It is to substitute the current diesel imports by 30% thus helping the country in saving foreign currency which is currently used to import diesel.